MIDWEST Field Services was at an educational facility in the Western United States performing inspections and testing of 15KV load break switches and indoor dry type transformers. The services were being performed as part of an insurance claim. The electrical distribution system had experienced a failure of some components within the system and the customer was having issues after replacing the damaged components and re-energizing the system. Our services included but were not limited to performing hard-focused inspections, making minor adjustments to mechanisms, performing insulation resistance testing, contact resistance testing, and winding resistance testing. No deficiencies were found with any of the equipment so all of the cover panels were installed and the equipment was energized. It was at this time that the transformers secondary phase-to-phase and phase-to-ground voltages were measured and found to be fluctuating by as much as 50% below the expected voltage. The equipment was shut down and the 15KV fuses for each of the load break switches were removed and the internal resistance was measured. The manufacturer has a range for this fuse between 24.871 mΩ and 33.6 mΩ. The fuses that were in service had resistance values that were nearly twice the manufacturer’s maximum tolerance. These fuses were replaced with fuses that were within the manufacturer’s resistance tolerance and the equipment was again energized. The secondary voltages for all of the transformers were again measured and found to be constant and within 1% of the nominal voltage. One of the original 15KV fuses was opened up and found that the fusible link inside was connected by a small fragment of its original configuration. The fuses were literally holding on by a thread inside which caused the increased internal resistance and translated into the erratic voltages seen on the secondary of the transformers. Long story short, the entire electrical distribution system was exposed to the short circuit and while other components ultimately failed this event reinforced that the electrical stresses were experienced by the entire distribution system and caused other components (fuses in this instance) to be compromised to the point they were unacceptable for continued service.
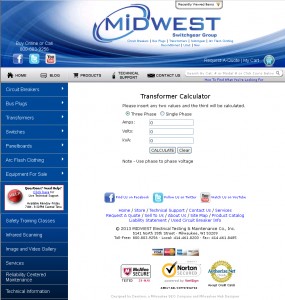
Transformer Calculator to help customer decide what transformer they need for specific load.
MIDWEST’s web site has a “Transformer Calculator” to help customers decide what transformer they need for specific load. We are frequently asked by customers to help them determine what size transformer they need to replace an existing power transformer. The Transformer Calculator uses voltage, current, and Kva. If you have any two, it will calculate the third value. This allows the user to quickly see what happens if they make some changes. We had a customer ask about a Square D 50 Kva, 480 volt to 208/277 volt dry type transformer. When we discussed their load needs and diversity, they decided they needed a 75 Kva transformer instead, based on their present and expected future load. This is a common occurrence. By having access to the power transformer calculator, you can play with the numbers yourself. The usual variable is current, aka load, amps, juice. The voltage is usually a known, fixed value. So by calculating existing load and estimating future load, you can quickly estimate the size of the transformer you might need, in Kva, by using the Transformer Calculator. We also suggest having at least 20% excess capacity. Quick tools such as this should not be used for design purposes. That needs to be left up to experts.
MIDWEST’s Switchgear Technical Center is always busy, but sometimes it can be extremely busy, loud and a little wild with the cross talk between the technical work stations. To an outsider, the noise, excitement, fast technical jargon and obvious intensity might make them wonder how anyone could function in such an environment. It would certainly drive the meek crazy. But the Engineers and Techies love the action. It can vary from the urgent to the absurd. Here’s an example of two separate but simultaneous energized conversations between MIDWEST’s Switchgear Technical Center and two customers. Each of the two conversations sounded almost exactly the same. Both conversations were about reconditioned or new oil filled electrical power transformers. 50 Kva oil filled 480 to 240 volt transformers and a 50 Mva oil filled 13,200 volts to 138 Kv GST transformer. One small oil filled transformer and one massive oil filled power transformer. Both conversations had a sense of urgency, one days and the other months. Both had a steady stream of technical details, a time table, preparation, freight, trucking, tests, some frustrations, as MIDWEST ground through each detail, double checking and confirming them one by one. A listener might think they were selling the same thing. They sound alike. 50 Mva and 50 Kva. Actually they were, oil filled electrical power transformers. But one was electrically a thousand times larger than the other. 50,000 Kva and 50 Kva. Just another day in the technical world.
What is the hardest part of a project to furnish and install a 75 MVA GST Power Transformer? Like most difficult questions, the immediate answer is, “It depends.” As someone who has actually worked in the field on switchgear and transformers, I think the hardest part is getting the transformer to the final installation site, especially if the site is in South America. Getting it from the manufacturing floor to the installation site and on the pad without any bumps, so to speak. This is a huge worry because things can happen that are out of your control. At least on the manufacturing floor and at the installation site, you usually have total control. Performing the engineering, specification, physical design, and identifying auxiliary devices can be tedious and requires diligence. Commissioning on site is a lot of work and there are plenty of opportunities for things to go wrong. But you are in control, except for the weather. The really big worry starts when that 75 MVA transformer leaves the manufacturing plant door for South America; gets transported to the exporting site; ships over a lot of water to the destination dock; gets unloaded; then gets transported overland again to the construction site; and finally gets rigged and craned on to the concrete pad. And all this action is monitored with an attached, very sophisticated, “Impact Recorder” that monitors and records bad things that may happen to the transformer from the time is leaves the manufacturer to the time is rests on the pad, one ocean and 1000s of miles away. At the end of the trail, so to speak, the data on the monitor is downloaded to a computer and analyzed for the possibility of damage to the huge and very costly mega VA GST Power Transformer. Nerve wracking. So, I vote transportation to be the hardest part of a project involving large MVA Oil Filled Power Transformers.